宽度800mm-1250mm
厚度0.15mm-1.0mm
磁感1.7
叠片300
涂层A、Z、H、M、J、K
是否切边切边、不切边
包装精包装
无取向电工钢制造工艺
生产具有高斯织构的硅钢,关键在于利用二次再结晶。为了实现二次再结晶,通常需要在合金中添加正常晶粒长大抑制剂,如MnS等。晶粒长大抑制剂必须能以参杂的形式弥散地分布在合金基体内,在二次再结晶发生时,能够有效地阻止基体晶拉的正常长大,同时,又要求在后的高温退火中可方便地消除掉,以免恶化产品的磁性能。在二次再结晶中、二次晶粒长大的取向核主要依靠适当的冷轧工艺和再结晶退火来产生。由于相变会破坏晶粒取向,因此在热处理过程中保持单相至关重要。
目前存在的可能影响无取向电工钢质量的潜在问题如下。
1、铸坯浇注质量。铸坯易产生边裂;浇注过程辊缝收缩程度大,使铸坯受到夹持力,内部质量不佳。
2、带钢表面氧化铁皮较重。相对比传统工艺,薄板坯流程表面氧化铁皮更难去除,除鳞水压力高达40MPa。对硅含量较高的无取向硅钢,氧化铁皮较其他钢种更难去除。
3、瓦楞状缺陷。尽管薄板坯工艺能改善铸态组织,提高等轴晶比例,但总体晶粒细小。尤其是在低碳(<50ppm)、硅较高(≥1.7%)的牌号(约50W470及以上牌号)的无取向硅钢薄板坯连铸过程中无电磁搅拌,导致柱状晶比例高。且热轧过程中无相变,细小柱状晶难于被破碎,产生纤维状组织,并遗传至后工序乃至成品表面产生几微米宽的瓦楞状缺陷。这也成为薄板坯连铸连轧流程生产无取向电工钢产品结构过程中亟待解决的一个关键问题。
4、夹杂物尺寸。从目前薄板坯连铸连轧生产的实践经验来看,此流程由于夹杂物含量较高和热轧板中第二相析出物尺寸较传统流程略小,与无取向电工钢工艺控制过程中希望热轧板中杂质元素尽可能以粗大第二相的形式存在的原则相悖,因此在生产更的无取向电工钢(如高牌号及薄规格)难度更大。
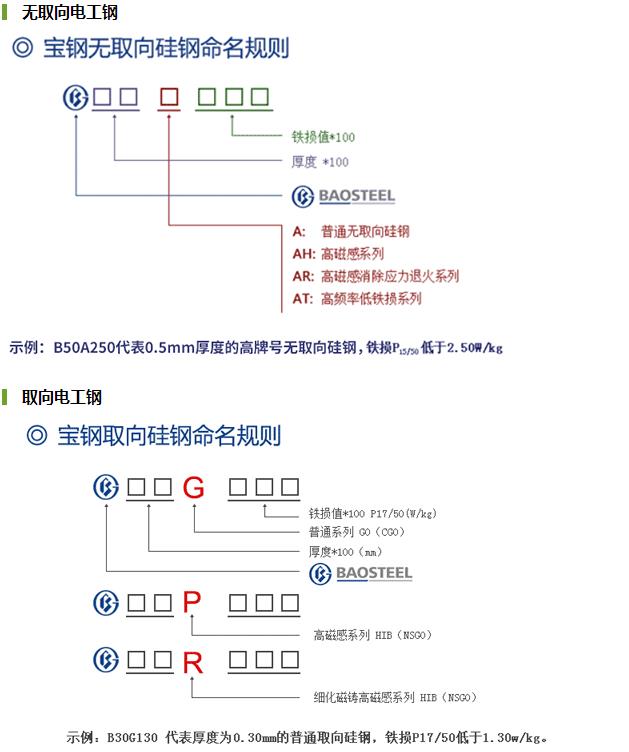
无取向电工钢的生产要求板坯加热温度不能过高,以防止第二相粒子重新固溶,并在热轧及后工序热处理过程中再次细小弥散析出,阻碍晶粒长大,恶化成品铁损。然而,又要求终轧温度相对较高,有利于第二相粒子的粗化聚集,促进晶粒的长大,改善铁损。因此,板坯加热温度一般控制在1150℃左右,而终轧温度控制在850-950℃。这对看似矛盾的生产控制原则在传统厚板坯工艺流程中因精轧前粗轧环节带来的大幅温降而难以实现。而薄板坯连铸连轧流程在此方面有固有优势,并且由于省去了粗轧环节,使终轧温度精度也得到更好控制,带钢磁性更加均匀。
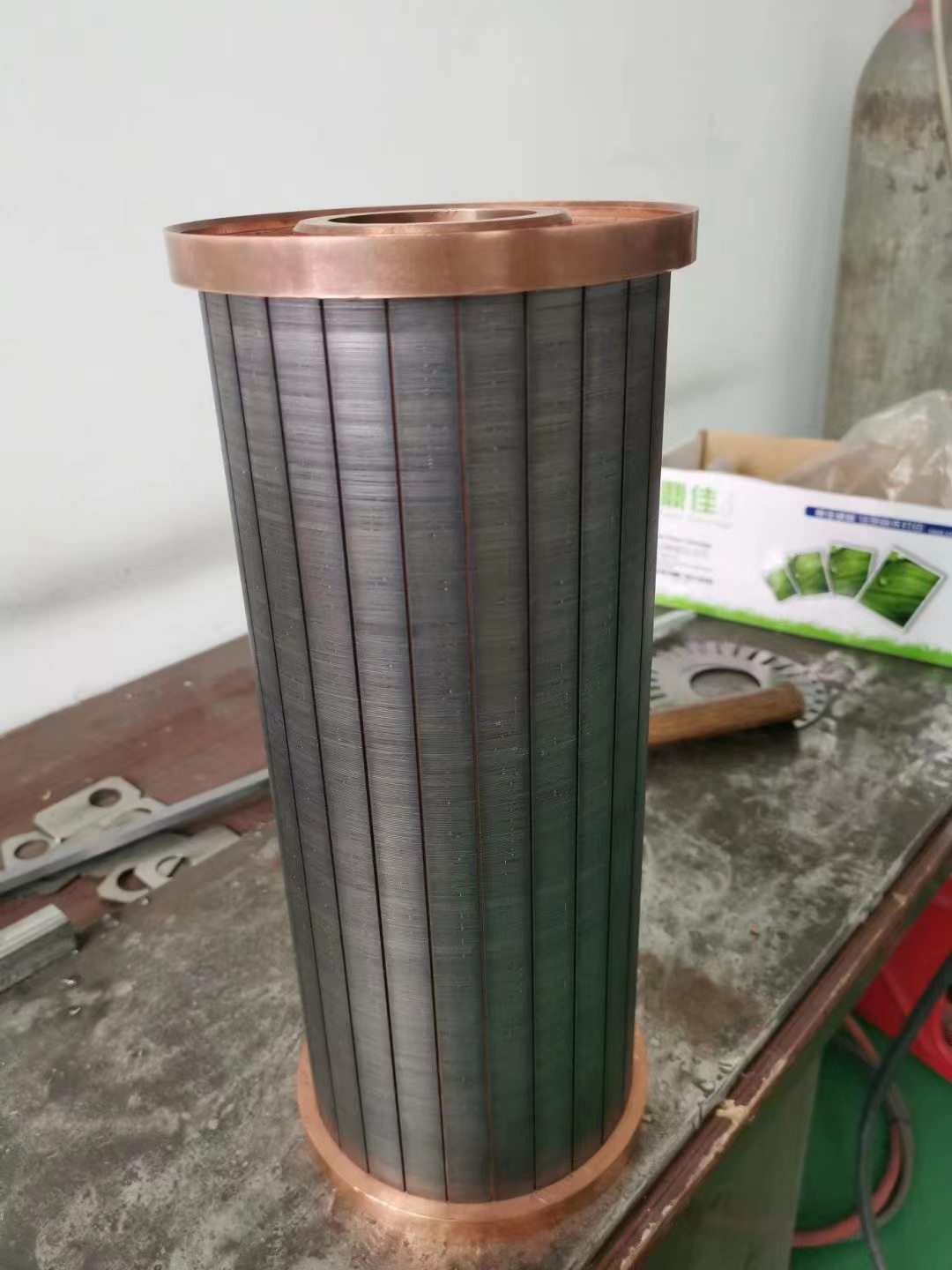
无取向电工钢冷轧工艺
热轧板常化和酸洗后应尽快冷轧,如果停放时间长,钢中固溶碳和氮析出形成不稳定第二相,使冷轧时碳和氮钉扎位错作用减弱,退火后再析出的AlN尺寸增大,磁性降低。
1、以AlN为主要抑制剂的大压下率冷轧法;
2、以MnS为主要抑制剂的二次冷轧法。
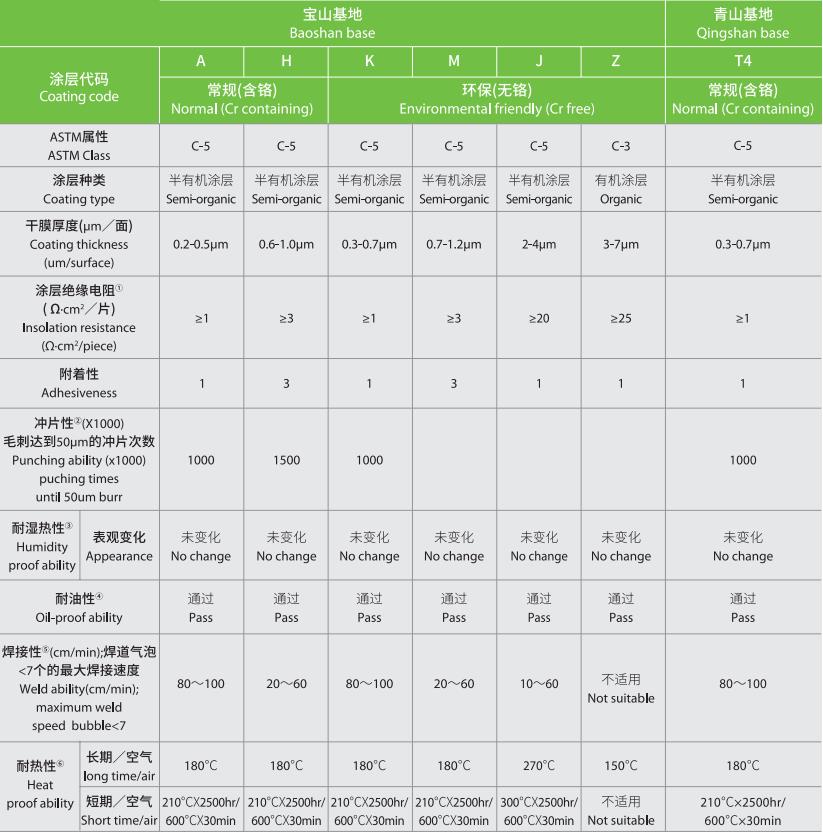
电工钢市场尤其是无取向电工钢领域竞争日益激烈,合格的磁性能已无法满足用户的需求,成品板形及表面质量已成为产品竞争的重要因素。薄板坯连铸连轧流程由于带坯断面温度均匀,纵向温度波动小,热轧板板形和尺寸控制精度更高。热轧原料尺寸质量的提升,为冷轧生产提供优异条件。提升冷轧后产品质量,使终成品叠片系数提高,更好满足下游用户的需求,提高市场竞争力。
我们本着“以信为天,以诚为本”的经营理念为宗旨,用热忱、优良的服务,让顾客满意。坚守“以人为本、以诚取信、以质取胜、以新争天下”的质量方针和“正正直直做人,踏踏实实做事”的企业精神。
http://www.yuyuansteel.com